VFD Operation
A VTdrive® VFD comprises three major power sections, i) a rectifier, ii) a DC filter and iii) a three phase inverter. The noise is primarily generated by the inverter section. The inverter section operates by chopping up the DC bus voltage (typically around 570Volts DC) and creating a PWM output voltage that causes an average sinusoidal current of variable frequency to flow through the motor. In modern inverters, the PWM waveform is generated by IGBTs operating as switches, so they are either turned fully ON or fully OFF. On each phase, there are two switches in series and across each switch, there is a flyback diode.
There is a transition period between the ON state and the OFF state, and the OFF state and the ON state. This is referred to as the switching state and has inherent switching losses.
There are three phases out of the inverter, each phase is generated by two switching devices, one from the output to the negative DC bus rail and the other to the positive DC Bus rail. This gives a total of six switching devices that are being controlled to produce the PWM output waveform. Switching or carrier frequencies are typically in the range of 1kHz to as high as 16 kHz.
For each cycle of the switching frequency, there are three positive transitions and three negative transitions resulting in transients occurring at six times the carrier frequency. These switching transitions are effectively phase modulated by the PWM waveform so the noise is aperiodic or semi random in nature. During the ON state, a switching element carries the output current for that phase and has an ON state voltage of between one and three volts depending on the device and current. Power dissipated in the switching element during the ON state is known as a static loss. When the device begins to turn OFF, because it is carrying an inductive current, the voltage across the device is driven to the opposite rail voltage and the current not passing through the switching device, is driven through the flyback diode on the opposite switching device. The voltage across the switching device during the switching OFF period is in the order of 600V with the current through the device reducing from 100% to 0% over the period of the switching. At switch OFF, there is a very high switching power dissipated (600V x 0.5 x Io x Ts). The slower the switching time, the higher the switching losses.
Modern IGBTs are able to switch from ON to OFF in periods as low as 100nS. There is a tremendous thermal advantage in “fast” switching resulting in smaller silicon, smaller heatsinks and lower costs. The disadvantage of high speed switching, is that the noise bandwidth is much greater. The operation of switching current ON or OFF results in the generation of electromagnetic noise. The bandwidth of that noise is a function of the switching time (Time of transition from ON to OFF). This is well accepted as a cause of Electromagnetic Interference.
When the IGBTs are switched ON and OFF, there are leakage currents to earth caused by stray capacitance within the VFD and external to the VFD.
In older VFD designs, there was no decoupling of the DC bus to the chassis. In these cases, the high current noise transients are conducted via the earth connection to the outside world and then via capacitance in the wiring and other equipment, to the phase wiring and back to the DC bus via the bridge rectifier. Modern designs that comply with the European requirements include decoupling between the DC bus and the chassis to provide a return path back to the DC bus. (completing the circuit.)
The traditional EMC conducted emissions tests do show the effects of the noise generated by the stray capacitance within the VFD and the rapid switching voltages. The amplitude of the noise transient current is a function of the value of the stray capacitance and the rate of rise of voltage (dv/dt). The length of the current pulse is a function of the DC bus voltage and the dv/dt. It is imperative that the design of the decoupling offers a very low impedance path across the full spectrum of the noise generated in this circuit. Poor designs will fail the conducted emissions test. This mechanism is exactly the same mechanism that occurs in switchmode power supplies, but in small switchmode power supplies, it is possible to isolate the heatsink from earth and reduce the transient noise currents flowing in the earth circuits.
Conducted Emissions.
In a practical VTdrive® VFD installation, the output of the VFD is connected to the windings of the motor via a length of cable.
The voltage applied to the motor is a PWM waveform generated by the inverter section of the VFD with fast rising and falling edges.
There is considerable capacitance between the stator windings of the motor and the motor frame and just as the stray capacitance in the VFD causes noise currents in the chassis of the VFD, the capacitance within the motor causes high noise currents to flow between the motor windings and the frame of the motor.
The noise current spectrum covers the frequency range from KHz to tens of MHz.
The circuit is closed by conductive paths from the motor frame back to the DC Bus of the VFD.
One path, is the return earth path provided by the wiring between the motor and the VFD. Current will flow on the earth conductor between the motor frame and the VFD frame and via the DC decoupling back to the DC Bus.
There is considerable capacitance between the stator windings of the motor and the motor frame and just as the stray capacitance in the VFD causes noise currents in the chassis of the VFD, the capacitance within the motor causes high noise currents to flow between the motor windings and the frame of the motor.
The noise current spectrum covers the frequency range from KHz to tens of MHz.
The circuit is closed by conductive paths from the motor frame back to the DC Bus of the VFD.
One path, is the return earth path provided by the wiring between the motor and the VFD. Current will flow on the earth conductor between the motor frame and the VFD frame and via the DC decoupling back to the DC Bus.

Another path is back to the DC bus via capacitance between the incoming three phases and earth to the incoming three phases and then through the rectifier to the DC bus.
The conductors between the motor and the VFD have an impedance that is made up of resistance, inductance and capacitance. At high frequencies, due to skin effect, the current flows on the surface of the conductor. At 100KHz, most of the current is concentrated in the outer 0.2mm of the conductor. With a circular conductor, this can increase the effective impedance of that conductor dramatically relative to the DC impedance of the cable.
If we look at the circuit between the output of the VFD and the motor, we have a phase impedance Zp and an earth return impedance Ze. In series with this we have the impedance of the motor capacitance Zm and this is very low at high frequencies.
If we look at the circuit between the output of the VFD and the motor, we have a phase impedance Zp and an earth return impedance Ze. In series with this we have the impedance of the motor capacitance Zm and this is very low at high frequencies.
The voltage that appears on the frame of the motor where it is totally isolated, is determined by the potential divider comprising Zp plus Zm plus Ze. The voltage being the ratio of (Zp +Zm)/(Zp + Zm + Ze). In some cases, the size of the earth conductor is half the size of the phase conductor so the impedance of Ze is up to twice Zp. The impedance of the capacitance can be very low relative to Zp, so it is possible for the noise voltage to be hundreds of volts on a 400 volt motor frame.

When the motor is physically installed, there are many other paths between the motor and the DC bus of the VFD. Some of these paths are direct through the installation from the motor frame to the VFD frame, and others will be through the installation via other capacitance to the phase conductors and then through the rectifier back to the DC bus.
Current will flow in all paths, the magnitude of the currents is a function of the “stray voltage” on the motor frame and the individual impedances of the other paths.
Current will flow in all paths, the magnitude of the currents is a function of the “stray voltage” on the motor frame and the individual impedances of the other paths.
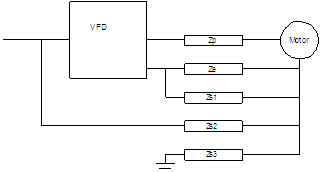
“Stray” or “Leakage” currents, flowing through the installation cause “stray” noise voltage to be developed and induced in other circuits and this can result in problems with the operation and integrity of other equipment. These voltages have been measured in some installations at levels in excess of 100 volts peak and have caused failure of equipment such as switchmode power supplies and flow meters. There can be significant energy in these stray voltages with MOVs being damaged by the voltages.
The noise can cause interference with the operation of equipment, blocking serial communications circuits, inducing resets in microprocessors and false input operations on electronic equipment.
Motors can be started and stopped intermittently by extraneous noise voltages which are well in excess of the EMC immunity requirements.
Stray voltages in sensitive areas such as cow sheds can have a severe effect on the health and behaviour of the cows with documented evidence of issues caused by stray voltages.
Recent cases have come to light of severe herd mastitis, loss of production and elevated cell counts caused by VTdrive® VFD induces stray voltages.
The noise can cause interference with the operation of equipment, blocking serial communications circuits, inducing resets in microprocessors and false input operations on electronic equipment.
Motors can be started and stopped intermittently by extraneous noise voltages which are well in excess of the EMC immunity requirements.
Stray voltages in sensitive areas such as cow sheds can have a severe effect on the health and behaviour of the cows with documented evidence of issues caused by stray voltages.
Recent cases have come to light of severe herd mastitis, loss of production and elevated cell counts caused by VTdrive® VFD induces stray voltages.
There are additional stray capacitance paths between the cable and the environment through which the cable passes. This includes capacitance to other conductors and to earth and structures.
The cable capacitances also cause stray noise currents to flow in other circuits.
The cable capacitances also cause stray noise currents to flow in other circuits.
没有评论:
发表评论